2019年10月16日下午,由伊萊特能源裝備股份有限公司制造的“直徑15.6米奧氏體不銹鋼鍛環(huán)”從該公司成功發(fā)運,標(biāo)志著伊萊特制造的2件全球最大整體鍛環(huán)正式完成。
記者從現(xiàn)場看到,運送該整體鍛環(huán)的拖車共有48個車輪,操作人員可以對車輪的轉(zhuǎn)向及拖車的前后高度進行獨立控制。整個拖車運輸時需要占用5個車道,在公安交警部門的護送下,這件大國重器高高聳立,沿途車輛和群眾也紛紛投來好奇的目光,整個運送過程煞是壯觀。
直徑15.6米奧氏體不銹鋼鍛環(huán),由伊萊特與中國原子能院、中科院金屬所李依依院士團隊共同研發(fā),從2016年項目立項開始到正式交付總計花費了近4年的時間,期間項目團隊先后完成2米、5米、等截面模擬件;直徑16米設(shè)備能力驗證件;一件直徑15.6米等比例試驗,以及2件直徑15.6米的正式工程件。這一項目打破了三個世界紀(jì)錄:
一是首次實現(xiàn)230噸級金屬坯分級構(gòu)筑,增材制造;
二是成為單體最重的奧氏體不銹鋼鍛件;
三是成為直徑最大的奧氏體不銹鋼整體鍛環(huán)。
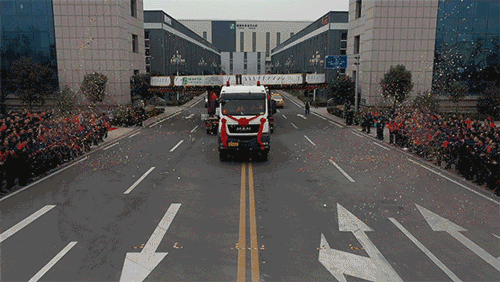
該項目采用了國際先進的綠色鍛造技術(shù),即使用“增材制造+近凈成型”的方式,在極大減少材料、能源的消耗的基礎(chǔ)上,同時提高了超大型鍛件均質(zhì)化制造地難題,具備世界領(lǐng)先水平。
所謂增材制造,是指不同于傳統(tǒng)大鍛件使用的原材料,本次整體鍛環(huán)制造使用了一項李依依原始團隊首創(chuàng)的“金屬構(gòu)筑”技術(shù),研發(fā)團隊為每個鍛環(huán)使用了50多塊小型板坯,經(jīng)過特殊焊接,在高溫高壓狀態(tài)下,讓這50多塊獨立的小型板坯重新“生長”成為一塊整體的原材料,由于小型板坯制造時更容易控制,更容易做到均質(zhì)化,這一技術(shù)成功避免了傳統(tǒng)百噸級大鋼錠制造時經(jīng)常遇到的元素不均、中心疏松、縮孔等問題,鍛件質(zhì)量也隨之得以更高。
而近凈成型制造,顧名思義就是鍛件的毛坯接近于最終成品,使用近凈成型加工的優(yōu)點是材料損失少,能源消耗少,加工周期縮短。本次整體鍛環(huán)使用的軋環(huán)機也是全球同類設(shè)備中最大的一臺。而按照傳統(tǒng)技術(shù),如此大尺寸的工件只能使用分段焊接的方式。但本次制造,由于使用了近凈成型、整體軋制的技術(shù),整個工件一體成型,近50米的工件周長上沒有一道縫隙,避免了焊接部位存在的不確定性,從而使整個工件的可靠性得以大大提高。
據(jù)了解,這件超大鍛環(huán)將用于我國最新的核電技術(shù)中,在其上邊將承受反應(yīng)堆7000噸的構(gòu)件重量,可以說是整個反應(yīng)堆的基礎(chǔ)。而這一產(chǎn)品本身也打破了三個世界紀(jì)錄:一是在世界范圍內(nèi)首次實現(xiàn)200噸級金屬坯的分級構(gòu)筑,增材制造;二是成為世界單體最重的奧氏體不銹鋼鍛件;三是成為世界直徑最大的無縫整體鍛環(huán)。這也標(biāo)著著我國在材料構(gòu)筑制備和超大鍛環(huán)制造上進入國際領(lǐng)先水平。